Industrial robots generally include the following:
What is a 6-axis Robot?
Six-axis robots are a type of articulated robot and the most common for industrial manufacturing. They provide the flexibility, strength, and reach needed to complete most applications including welding automation, material handling, material removal, and painting. Six-axis robots are able to move in the x, y, and z planes. In addition, they can perform rotational movements. This makes the movements of these robots similar to that of the human arm.
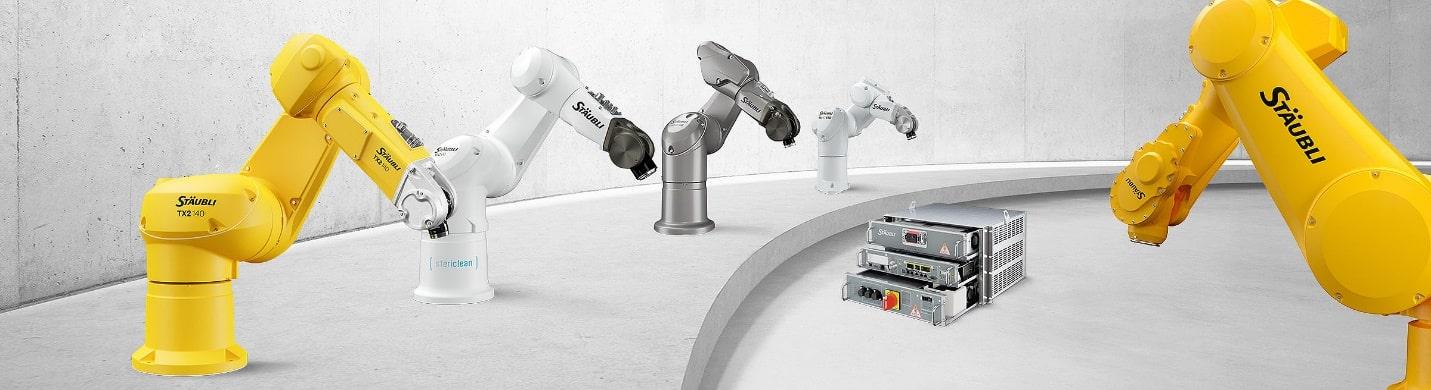
Six-axis robots are able to perform more types of robotic applications since they have an additional range of motion. Each axis represents an independent motion or degree of freedom, that allows a robotic arm to move to a programmed point.
There are several types of six-axis robots. They can vary from small to large. Their load capacity may be only a few kilograms to more than a thousand kilograms. They also have different access levels. There are even special six-axis robots designed for special work environments such as very clean rooms to casting environments.
What is a Delta Robot?
Delta robots were originally created in the 1980s but did not start to gain notice in the manufacturing world until about ten years ago. Now delta robots can be commonly found along many assembly lines across numerous industries. These robots are also known as parallel-link robots due to their parallelogram arm design. Delta robots typically have three to four carbon-fiber, lightweight arms that extend downward from the main robot body. Because of this design they are often referred to as spider robots with the spider-like resemblance of their arms.
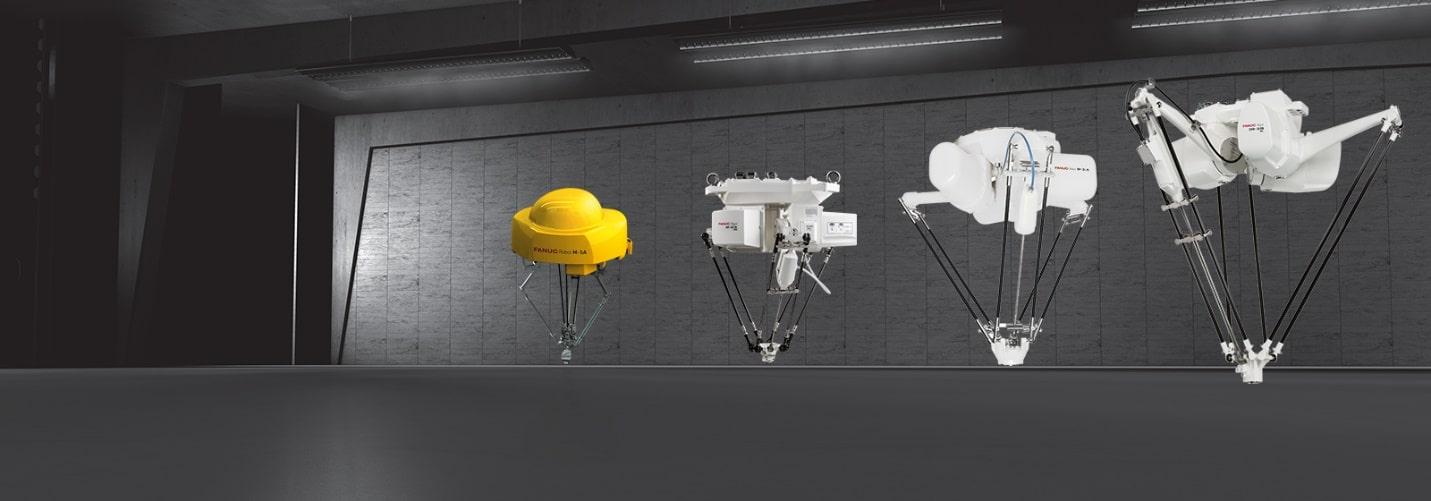
Delta robots are known for their high speed and high accelerations. Their design is what makes them speedier than other types of industrial robots. Most industrial robots have motors located in the robot arm, making them conducive for heavier payload applications. However, having the motors in the robot arm adds additional weight and prohibits fast speeds. With delta robots all motors are located in the main body above the work area. This keeps all the main weight of the robot stationary. All movement comes from the extremely light robot arms, allowing for low inertia for incredibly fast operating speeds and accelerations.
What is a Scara Robot?
SCARA Robots are a popular option for small robotic assembly applications. SCARA is an acronym for Selective Compliance Articulated Robot Arm, meaning it is compliant in the X-Y axis, and rigid in the Z-axis. The SCARA configuration is unique and designed to handle a variety of material handling operations.
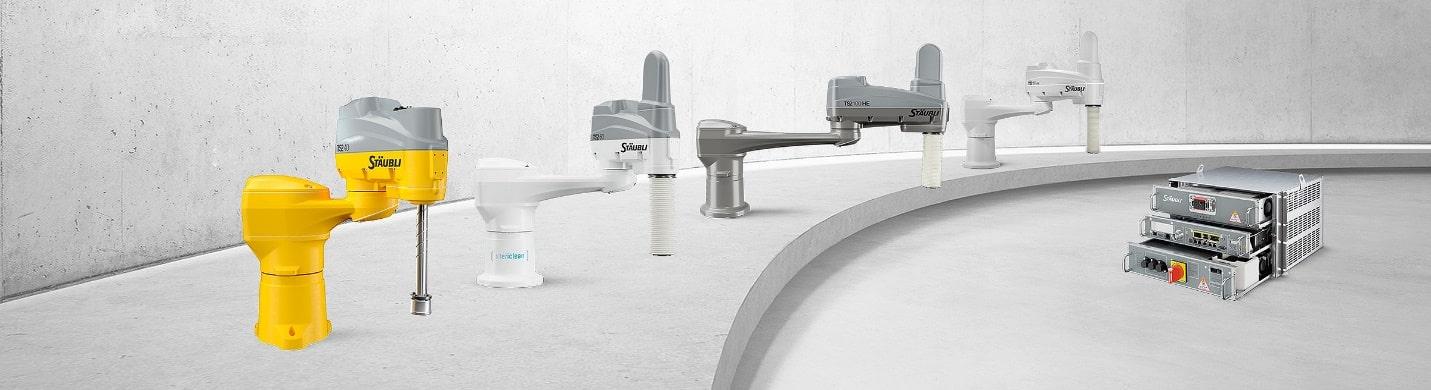
SCARA robots, also known as Selective Compliance Assembly Robot Arm or joint robotic arm, which are one of the most common forms of industrial robots in today’s industrial field. SCARA robots are suitable for mechanical automation in many industrial fields, such as automatic assembly, painting, handling, welding and so on.
What is a Collaborative robot?
Collaborative robots are defined as robots capable of safely operating around humans without the need for features such as safety fencing. Collaborative robots are also commonly referred to as cobots for short and are designed with collision avoidance technology. This collision avoidance technology is what allows collaborative robots to safely operate amongst humans. Their advanced safety sensors can detect when there is an intrusion within the cobots work envelope, and it will either slow its movement or stop all together depending how close a person or object may be.
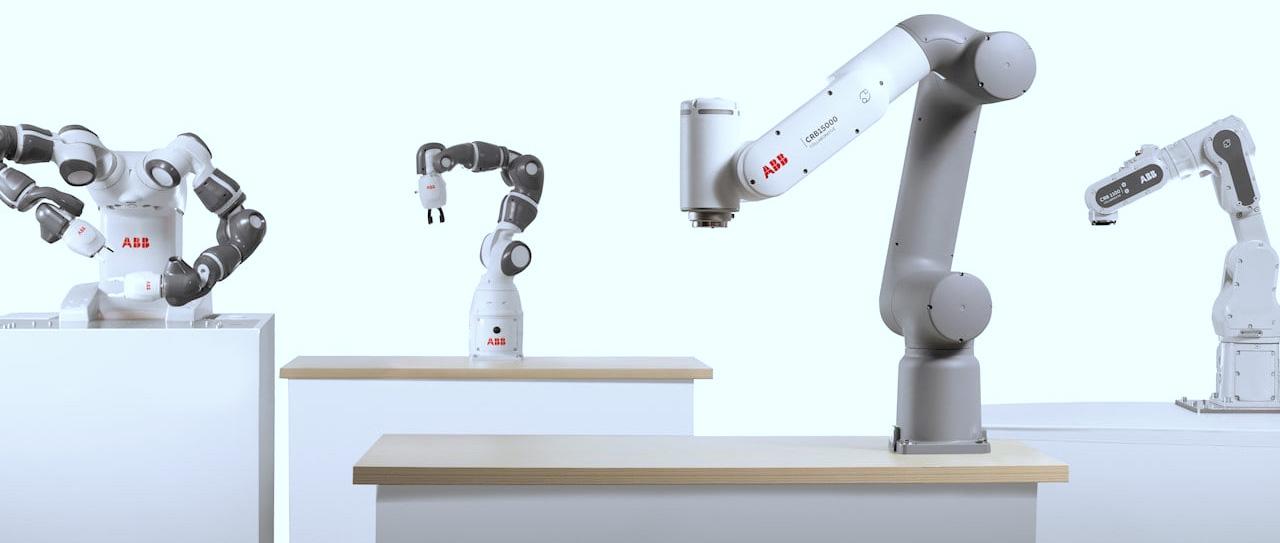
Another unique feature of collaborative robots is their ability to be programmed using hand guidance. With hand guidance integration is a breeze as cobots can be taught program positions and paths by simply moving the robot manually in the desired directions. The collaborative robot is then able to replicate the exact path or position it was shown. Collaborative robots provide further manual dexterity with the ability to lift heavy objects manually.
The integration of collaborative robots alongside human workers on production lines has helped manufacturers increase productivity, improve quality, and provide greater flexibility within operations. The affordability and continuously improving safety technology of these robots is fueling the rapid growth of the collaborative robot market, which is projected to only increase in the years to come.
There are several robots from the top robotics manufacturers that according to the type of robot application, the desired robot can be selected from different manufacturers according to the price and quality. Sorin Farbod Company, considering the supply network, consulting in choosing the right robot, as well as the experience of implementing robotic projects with different brands, can guide you in making better decisions regarding robotic projects.
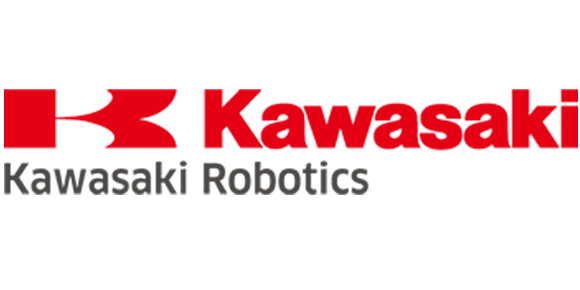
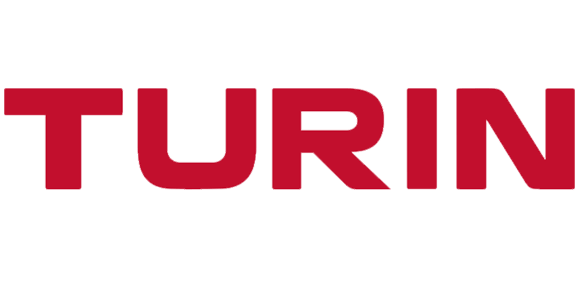
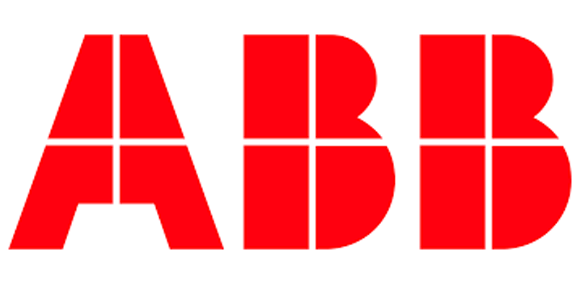
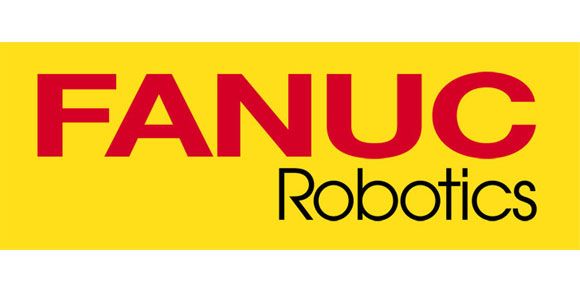
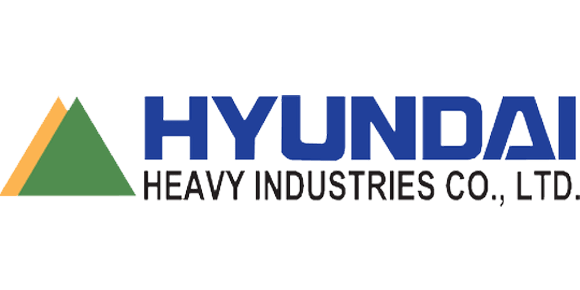
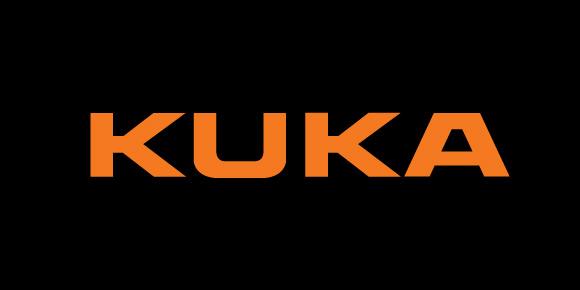
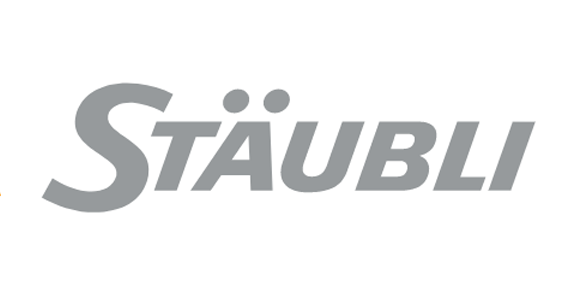
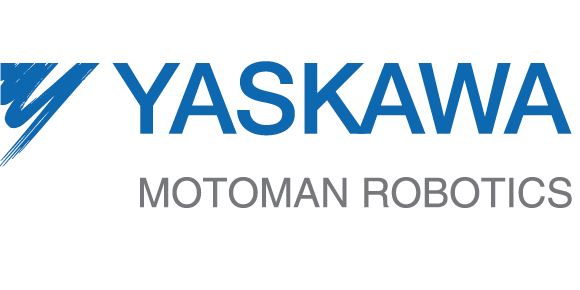